Wondering what lean project management is—and what it can do for your organization?
With a focus on fixing problems and reducing inefficiencies, lean project management is becoming increasingly popular across a number of industries. Lean principles were originally developed and used exclusively in the manufacturing world, as the principles promote simplified processes and emphasize high-quality output. This approach is particularly important for the production of goods, but has been so successful that it's been co-opted by other industries.
That being said, lean project management isn’t the right fit for every organization. In this article, we’ll explore the basics of this methodology to help you determine if it’s a good option for you, including a thorough definition, how to implement it, and some advantages and disadvantages associated with its use. And because no project should go untracked, we’ll also show you how project management software can be used to support lean in practice.
Let’s get started!
Table of Contents: Lean Project Management For Beginners
- What Is Lean Project Management?
- Implementing Lean Project Management
- The Benefits & Considerations Of Lean
- How To Implement Lean Project Management With Software
Chapter 1: What Is Lean Project Management?
.webp)
The term “lean” doesn’t apply solely to project management. Generally, it is a way of thinking that focuses on lean operational management, which is grounded in efficiency. Although the concept is a combination of Western (U.S.) and Japanese cultures and practices, the origins of lean can be traced back to the Toyota Motor Corporation during the post-World War II era.
Struggling with poor productivity, Toyota implemented the Toyota Production System (TPS) to remove problematic elements from its processes, namely inefficient processing, long wait times, inventory issues, and more. One of the core principles of TPS—which was all about the systematic removal of waste in an effort to improve efficiency—was just-in-time, or JIT. For Toyota, JIT meant getting just the right quantity of raw materials and producing just the right quantity of products to meet customer demand. In other words, production was closely tied to demand. The adoption of TPS and JIT represented a “lean” approach to manufacturing; it was a tactic that would ultimately make Toyota one of the most successful companies in the world.
At the time, TPS was a revolutionary concept that led to reduced lead times, decreased costs, and higher profit margins for Toyota, but what specifically made it work? Behind its success was the elimination of three kinds of process-related waste, known as the 3Ms:
- Mudra—activities that consume resources without increasing the end value
- Muri—overusing equipment or overworking employees beyond reasonable or practical limits
- Mura—operational “unevenness,” or irregular performance of work that increases costs and possibly decreases efficiency over time
By the 1980s, these principles started to migrate west when Western manufacturers realized that Japan was outperforming them. The name lean originated around the time of this migration, first being applied to manufacturing and later, to project management.
Lean Project Management Principles
Today, lean project delivery is all about maximizing value while minimizing waste—essentially, using a minimum amount of materials, equipment, labor, and space. In particular, lean methodologies optimize resource use by eliminating waste in seven areas:
- Overproduction—Excess production is unnecessary and leads to high levels of inventory; it also contributes to the other areas of waste.
- Waiting—Backlogs (waiting for things to be done) in any area leads to lost time.
- Transportation—Moving materials from place to place unnecessarily causes inefficiency.
- Defects—Quality issues can only be fixed by spending additional time, money, and resources.
- Motion—Too many unnecessary steps in a process extends production time.
- Inventory—Surplus materials increase storage costs and are rarely used.
- Overprocessing—Work that doesn’t add value to a product or process is wasteful and drives up costs unnecessarily.
The “recipe” the lean approach uses to identify and remove waste in these areas is made up of the following steps:
- Specify value. Determine the project’s value in the mind of the customer.
- Map the value stream. Analyze the creation process for the product or project to identify areas of waste, such as unnecessary steps or actions that tax resources or compromise quality.
- Create flow. Develop an improvement plan to eliminate the waste identified in the value stream.
- Establish pull. Move the project forward or create the product based solely on demand from the customer.
- Embrace continuous improvement. Regularly reassess the project process with the goal of eliminating waste and maximizing productivity and efficiency.
A number of lean project management methodologies have been developed based on these principles. The most popular ones are:
.webp)
The Deming Cycle
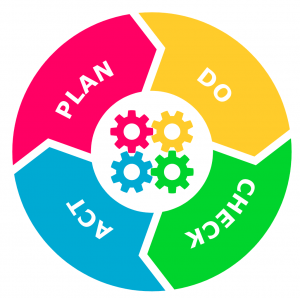
The Deming Cycle focuses on continually improving the quality of processes, products, or services through a logical sequence of four repetitive steps: Plan, Do, Check (Study) and Act. (It’s also referred to as the PDCA or PDSA Cycle.) Influenced by the scientific method, this quality improvement cycle gives project managers a framework for testing and analyzing potential process changes. (You can read more about it here.)
Six Sigma

Having a close resemblance to lean is Six Sigma, a management approach that focuses on reducing process variation and enhancing process control. While lean focuses more on waste reduction and Six Sigma focuses on removing process variation, the distinction between the two has blurred because of the many overlapping principles. The term "lean Six Sigma" is frequently used because some aspects of both approaches are required in order to produce positive results. (You can learn more about lean Six Sigma here.)
Kanban
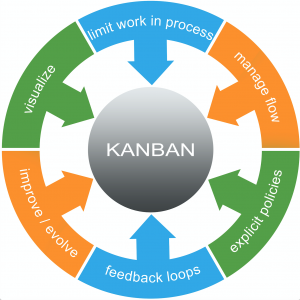
A popular framework used in agile software development, Kanban is considered a lean methodology. Work items are represented visually on a kanban board, allowing team members to see the state of every piece of work at any time. Users can gain insight on potential areas for process improvement by looking at board data on things like distribution of work, length of time to complete various steps, and problem resolution. Achieving process improvements with Kanban requires full transparency and excellent communication among team members. (Read more about it here.)
.webp)
Chapter 2: Implementing Lean Project Management
.webp)
Although lean project management is used in organizations of all types and sizes, it works best (at least to start) for small projects and small teams because it requires strong communication. As your organization grows, you can continue to nurture the lean mindset among new members.
The below presents an overview of the major phases associated with implementing lean project management:
1. Create a culture of ownership.
The traditional top-down approach doesn’t fit with the lean project management philosophy. While management ultimately takes full responsibility for products, processes, and business requirements, it is important for everyone to feel a sense of responsibility—and thus a sense of equality—when it comes to improving the way an organization works. Set a standard for openness and transparency to create an environment in which everyone is encouraged to identify problems and test solutions.
2. Establish a knowledgeable team.
There is no lean project management template that works for every project; application of the principles may not look exactly the same in every instance. That’s why it’s important to form a well-equipped team that has deep knowledge of lean project management values and is capable of keeping everyone focused. One way to increase your team’s knowledge of lean is to provide internal training sessions clarifying the procedures and methods around lean principles. You can also keep lean at the forefront by conducting periodic Kaizen workshops—process improvement sessions—that help teams get better at identifying and implementing changes.
3. Make lean improvements part of your culture.
A culture of improvement should permeate throughout your organization. Encourage and empower teams to look for continuous improvement everywhere. Self-motivated team members should be able to evaluate a process, take the steps to make improvements, or, if they see a real need, call in a designated "lean team" for bigger opportunities. Staying true to lean requires continuous attention.
Chapter 3: The Benefits & Considerations Of Lean
.webp)
Implementing lean project management is a long-term proposition—one that should (if done right) change the culture of your organization for the better. The benefits of lean project management include:
- Simpler processes. Continually refining your workflow means getting rid of wasteful activities; the end result is a simpler process that’s easier to manage.
- High-quality output. By cutting out valueless activities, your team can focus more on the tasks that lead to a better quality product; they’ll also make fewer mistakes.
- Motivated employees. Employees who spend time on meaningful work have a greater sense of purpose. Plus, employees who feel they are working together on a level playing field naturally take more initiative and are more dedicated to producing quality products.
- Smarter ways of working. Lean’s “pull” system allows employees to work on tasks as they are ready, so everyone’s working on the right tasks at the right time.
- More value for the customer. Focusing more on value-add work naturally produces a better product.
Done well, lean is capable of delivering all the benefits described above. But many companies struggle to implement lean project management in a way that produces meaningful results over the long term. The primary issues that tend to pose a problem for organizations are:
- A lack of time. Lean requires planning and time upfront. Mapping key product flows, creating improvement plans, conducting daily team meetings to discuss completed and outstanding work, and identifying problems are just a few things that need to be done regularly to keep the process flowing. Perceived as interfering with the usual work tasks, these activities often fall by the wayside as time goes by, making it impossible to follow through with lean.
- A lack of strategy. Some organizations get so focused on lean tactics that they lose sight of their overall strategic plan. To make the most of lean, you need to intentionally apply its principles to your existing corporate goals, asking, for instance, how it can help you increase sales or improve customer satisfaction. Use strategy software to set your course and determine which projects to execute on; then use lean to get things done more efficiently.
- Not enough buy-in. Lean is considered a radical way of thinking that requires complete buy-in from teams. You’ll need to devote a massive chunk of your efforts to changing people’s behaviors and encouraging them to work more independently. If you haven’t taken the time to educate your people on the new way of working and how it will benefit them, they aren’t likely to get on board. To help gain buy-in, invest in training programs that will teach people about lean and improve their communication skills, which are critical for success.
- Cutting things too fine. If there’s a bottleneck or your resources are too low, delays can pile up quickly. Create a contingency plan to provide some leeway, and use project management software to track tasks in real-time.
Chapter 4: How To Implement Lean Project Management With Software
.webp)
Like any other methodology, lean project management is best carried out with the support of software.
ClearPoint project management software gives teams a way to manage and track tasks and results, stay on top of project progress, and keep everyone on the same page. For teams using lean, ClearPoint can be especially helpful in optimizing resource use. Here’s how our project management software solves some of the challenges associated with process waste:
It helps avoid resource waste.
ClearPoint can automatically source data from other systems on a predetermined schedule (monthly, quarterly, or YTD); it also has a built-in calculation tool. Use it to track a variety of data types associated with your company’s past performance and perform sophisticated calculations that can help you select the most impactful projects (the ones that will most affect your strategy) and their progress. Trend dashboards visually display key metric performance over several periods, and users can easily drill down for more information on each metric. Doing so can help you avoid throwing excess resources at project challenges unnecessarily.
It reduces unnecessary waiting time for next steps.
Everyone on your team will spend less time chasing down data with ClearPoint’s Reporting Workflows. With Reporting Workflows, project leaders can create a page where users make regular updates to elements they are responsible for, which increases transparency around task progression. And our Workflow Emails makes it possible to automatically send out personalized instructions to all relevant individuals on how to make updates. Reporting Workflows eliminates the guesswork when it comes to next steps, and improves communication among team members.
It supports lean transportation.
Is your team inadvertently wasting time, resources, and costs by unnecessarily moving products and materials? Use ClearPoint to track key transportation metrics and identify specific areas of underperformance, whether related to timing, specific carriers, or anything else. You can track wait times between steps, and upload images and other visuals to allow the project team to stay on the same page for how your improvement suggestions might be practically implemented.
.webp)
.webp)
It can help reduce defects and process errors.
It can be difficult to pinpoint where defects occur in a production process—do they originate with the raw material or a specific piece of equipment, or are they due to human error? ClearPoint can track various elements of your production process to identify the cause of defects. Similarly, business processes are also subject to errors and wasteful task repetition. Reporting is one example; too many organizations waste time inputting data, sending emails, and creating reports. ClearPoint eliminates wasteful tasks associated with reporting by using automation.
Ready to start thinking lean?
No single project management methodology is perfect, which is why many organizations use some combination of methodologies. In the case of lean, its core tenet—minimizing waste while maximizing value—can still be applied to some degree even if you’re using another project framework.
To find out more about how ClearPoint supports lean project delivery, ask us to see it live—we’d love to show you around!